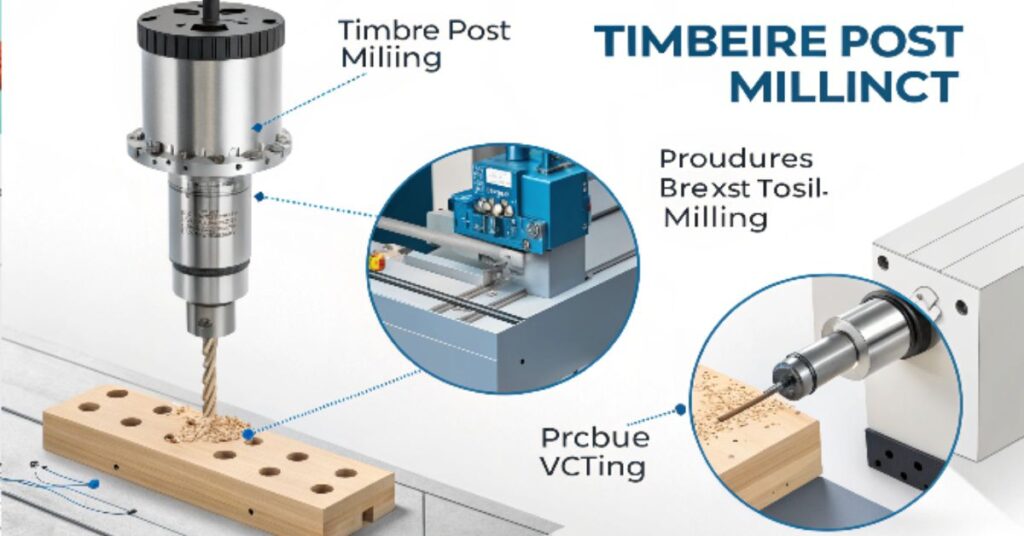
PCB (Printed Circuit Board) depaneling is the process of separating individual PCBs from a larger panel once they are manufactured. This is an essential part of PCB production, ensuring that each circuit board is ready for final assembly in electronic devices.
There are different methods to achieve this separation, each with its own unique advantages. Among the most popular techniques are Timbre Post, Milling, and V-Cut. Understanding these methods helps manufacturers select the most appropriate technique based on the design, cost, and production needs.
Understanding “Timbre Post” Method in PCB Depaneling
What is Timbre Post?
The term “Timbre Post” originates from French, referring to “postage stamps” due to their similar shape. In PCB depaneling, the Timbre Post method involves small, breakable tabs that hold the individual PCBs within a larger panel. These tabs can easily be separated by manual or mechanical means, making this method simple and cost-effective.
How Does the Timbre Post Work?
- Design Process: During PCB manufacturing, these tabs are integrated into the design of the panel. They create a grid-like structure that keeps the PCBs in place.
- Separation: Once the panels are produced, the individual PCBs are detached by breaking the tabs. This can be done manually or using automated machines.
Benefits of Timbre Post:
- Cost-effective for simpler PCB designs
- Easy to implement with minimal setup
- Suitable for lower production volumes
Challenges of Timbre Post:
- The edges of the separated PCBs may be rough
- Limited to less complex designs
The Milling Process: A Precise Approach to PCB Separation
What is Milling in PCB Depaneling?
Milling is a highly precise method used to separate PCBs. It involves the use of rotating cutting tools that carve out sections of the PCB panel to create individual boards. Milling is often preferred for complex and high-precision designs due to its accuracy.
How Does the Milling Process Work?
- Tooling: The PCB panel is fed into a milling machine where rotating cutters gradually remove material along the required separation lines.
- Precision: Milling machines are capable of handling intricate cuts, making them ideal for PCBs with complex shapes and smaller features.
Benefits of Milling:
- High precision for complex designs
- Suitable for both high and low volume production
- Can handle irregularly shaped PCBs
Challenges of Milling:
- Higher operational costs
- Slower processing time compared to other methods like V-Cut
- Requires more maintenance for the machines
V-Cut Technology: Efficient and Cost-Effective Depaneling
What is V-Cut Depaneling?
V-Cut, or V-scoring, is a popular technique where a V-shaped groove is cut into both sides of the PCB panel. These grooves are designed to weaken the board, allowing for easy manual or machine separation by snapping along the scored lines.
How Does V-Cut Work?
- Scoring: The machine makes V-shaped grooves on both sides of the panel. These grooves create a clear weak spot, enabling easy breakage.
- Manual Separation: After scoring, the panels are snapped apart by applying slight force, resulting in clean breaks.
Benefits of V-Cut:
- Fast and efficient for high-volume production
- Cost-effective, as it doesn’t require intricate tooling
- Ideal for straight-line separation
Challenges of V-Cut:
- Not suitable for irregularly shaped or complex designs
- May cause stress on the PCB along the scored lines, which can lead to damage if not done properly
How Timbre Post, Milling, and V-Cut Methods Work
Let’s compare how Timbre Post, Milling, and V-Cut each function during the depaneling process:
Timbre Post:
- Separation: Small tabs are broken to separate the PCBs.
- Edge Quality: Edges may require finishing.
- Suitability: Best for simple, low-cost PCB designs.
Milling:
- Separation: A rotating cutter removes material from the panel.
- Edge Quality: High precision with smooth edges.
- Suitability: Ideal for complex PCB designs with intricate features.
V-Cut:
- Separation: V-shaped grooves are created, and boards snap apart.
- Edge Quality: Clean edges, but stress may be introduced along the groove.
- Suitability: Efficient for high-volume production with straight-line separations.
Comparing Timbre Post, Milling, and V-Cut for PCB Depaneling
Efficiency Comparison
- Timbre Post: Best for low-cost production with simple designs.
- Milling: Highly precise but slower and more costly.
- V-Cut: Ideal for straight-line separations, offering efficiency at high production volumes.
Cost Comparison
- Timbre Post: Least expensive, with minimal setup costs.
- Milling: Higher cost due to specialized machinery and tools.
- V-Cut: Moderate cost, but offers faster processing for large volumes.
Advantages and Disadvantages of Each Depaneling Method
Timbre Post
- Advantages:
- Simple and cost-effective for basic designs.
- Can be used for small to medium-sized production.
- Disadvantages:
- Leaves rough edges that may require additional processing.
- Not suitable for intricate designs.
Milling
- Advantages:
- High precision, suitable for detailed designs.
- Capable of handling complex shapes.
- Disadvantages:
- Higher cost and slower than other methods.
- Requires more maintenance.
V-Cut
- Advantages:
- Fast and efficient for large-scale production.
- Cost-effective for straight-line separations.
- Disadvantages:
- Not suitable for complex shapes.
- Can introduce stress along the scored line.
Applications of Timbre Post, Milling, and V-Cut in Electronics Manufacturing
Each depaneling method has specific applications in the electronics industry:
- Timbre Post: Common in simple consumer electronics with low complexity.
- Milling: Preferred for high-precision electronics like medical devices or aerospace components.
- V-Cut: Widely used in mass production of consumer electronics like smartphones, TVs, and computers.
Factors to Consider When Choosing a Depaneling Method
When selecting a depaneling method, consider the following factors:
- Design Complexity: Choose milling for intricate designs.
- Production Volume: Opt for V-Cut for high-volume needs.
- Budget: Timbre Post is the most affordable for simple designs.
- Edge Quality Requirements: Milling provides the smoothest edges.
Safety Considerations in PCB Depaneling
PCB depaneling can pose safety risks, especially when using machinery. To ensure safety:
- Operator Training: Properly train operators to handle equipment.
- Protective Gear: Use safety glasses, gloves, and face shields.
- Machine Maintenance: Regularly maintain machinery to prevent accidents.
11. Future Trends in PCB Depaneling Methods
As technology advances, PCB depaneling methods are evolving:
- Laser Depaneling: Offers high precision with minimal mechanical stress.
- Automation: Increased use of robotics to improve efficiency and consistency.
- Eco-friendly Methods: Innovations to reduce waste and improve sustainability.
Frequently Asked Questions (FAQs)
Q1: What is the most cost-effective depaneling method?
Timbre Post is the most cost-effective method, especially for simple PCB designs.
Q2: Can milling be used for high-volume production?
While milling offers high precision, it is slower and less suitable for large volumes compared to V-Cut.
Q3: Is V-Cut suitable for complex PCB designs?
No, V-Cut is best for simple, straight-line separations and not ideal for complex shapes.
Conclusion
Choosing the right PCB depaneling method depends on various factors such as design complexity, production volume, cost, and edge quality. Timbre Post, Milling, and V-Cut are three common methods, each offering unique benefits and challenges. Understanding these methods helps manufacturers optimize their PCB production process for better efficiency and quality.